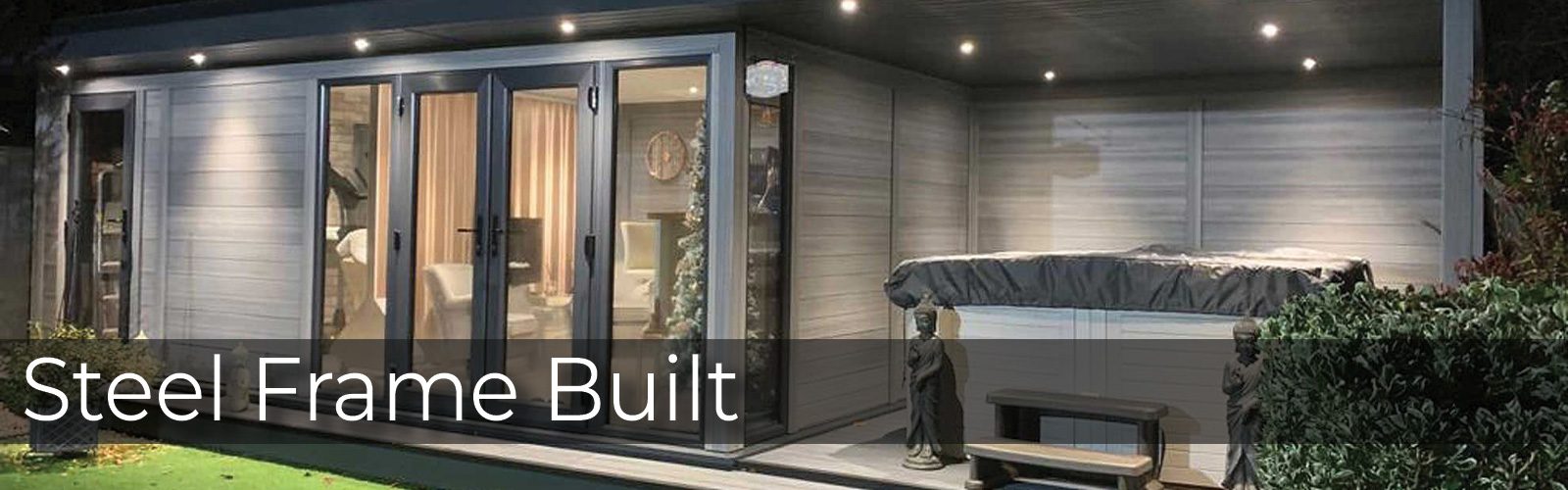
Steel Frame Built
Steel Frame Built
With the current housing crisis in the UK, fast, cost-efficient methods of construction are desperately needed. It is just one of the reasons that steel frame garden rooms have taken the home renovation market by storm.
More and more people are working from home these days. With remote working increasing across the country, a growing number of homeowners are converting spare rooms and garden sheds into offices.
Whether you need additional space for work, rest or play, as many consider an extension to the home, steel framed buildings offer an opportunity to save time and money.
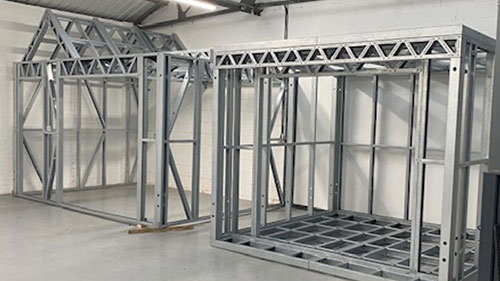
What Is A Steel Frame Garden Room?
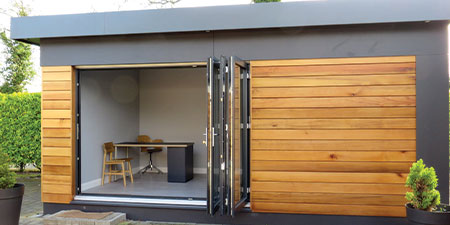
Garden buildings commonly use timber studwork to form a structural load-bearing frame. A steel frame garden room uses light-gauge galvanised steel instead of timber studs.
There are certainly advantages to steel framing, such as strength and speed of assembly, but there are also disadvantages. Read on for an unbiased look at the pros and cons.
The Benefits Of A Steel Frame Garden Room
Steel-framing may be a new technique in garden room construction, but it’s been a staple of building design for decades. Below we’ve outlined just some of the reasons metal frames are growing in popularity with garden office suppliers.
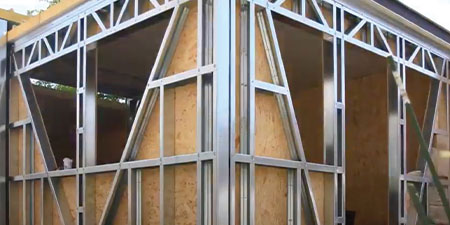
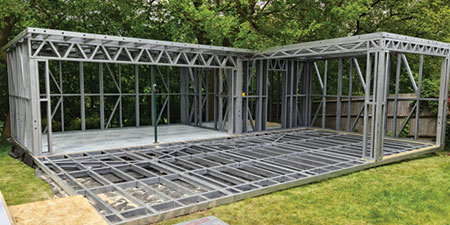
Strength
While timber is a strong building material, it’s no match for steel. Light gauge steel, also known as cold-formed steel, is far lighter and stronger than wood of equal size.
The added strength means there’s potential to use thinner joists in the floor and roof structure. Permitted development’s size limitations put ceiling height at a premium. Smaller beams can potentially add 2 – 3 inches of headroom.
Speed Of Assembly
Fully designed and fabricated offsite, metal frames need only be assembled upon arrival. They’re lightweight too, which makes them easier to transport and handle. In practice, the shell can be built in a matter of hours instead of days.
Faster assembly doesn’t just mean less disruption during the construction phase but also lower labour costs. While labour costs may sound like a concern for the supplier, they’re ultimately factored into the project, impacting the final price.
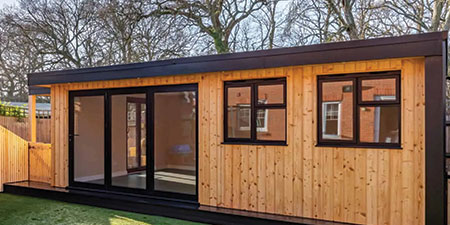
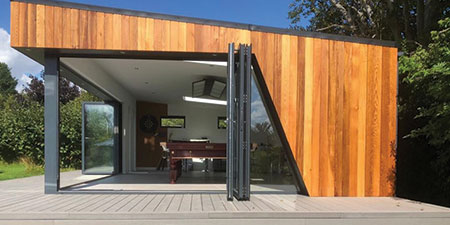
Long-Lasting
Simple, sturdy, and reliable – a metal frame won’t undergo the same rotting, warping, splitting, and cracking over time that a timber frame might. Steel frameworks aren’t vulnerable to pests or insects either.
Accuracy
We already touched on the fact that galvanised steel frames are designed and fabricated offsite. Suppliers use computer-aided design (CAD) tools to plan the framework. Structural calculations ensure the proposed garden room is solid and durable. Computer-assisted manufacturing (CAM) then turns those plans into a pre-fabricated structure accurate to within 0.5mm.
Stick built timber frames, by contrast, are measured and cut on-site. While the same degree of planning may go into a timber frame, it’s inherently less accurate.
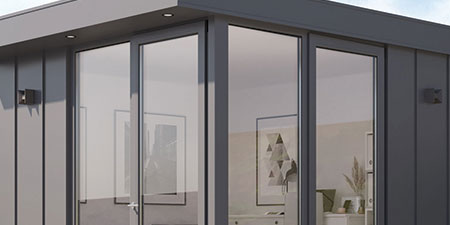
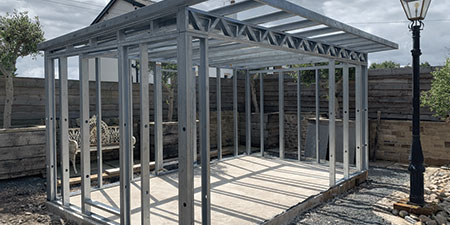
Cost
We’ve already mentioned labour costs, but they’re just one of the ways that steel framing is competitive with timber framing.
It’s no secret that timber prices have skyrocketed in the UK since the first lockdown in March 2020. Few people outside the construction industry recognise the scale of those price increases. Like all construction materials, steel has increased in price, but it hasn’t been subject to the same sort of rises as lumber. Timber has more than doubled in price, and ongoing shortages in 2022 mean that trend isn’t likely to change any time soon.
Beyond the raw cost of materials, steel results in less waste. Remember that you pay for waste twice: firstly, in the cost of the unused material, and secondly, in the skip to dispose of it.
Disadvantages Of Steel Framing
With all of the benefits we’ve highlighted, you may be wondering what the catch is. As is often the case, there are trade-offs to be made. Next, we’re going to look at what the disadvantages of a steel-framed garden room are.
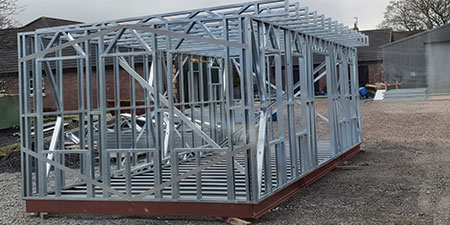
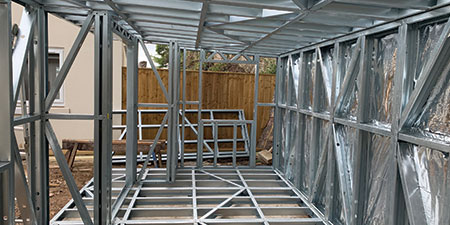
Fire Resistance
Many people will be surprised to see fire resistance listed as a disadvantage of steel framing. In fact, we’ve seen some suppliers tout the fact that steel doesn’t burn as a benefit over timber construction. Steel is indeed non-combustible; however, unlike timber, its structural integrity is quickly compromised by heat.
A fire can expose the steel frame to enough heat to cause it to buckle.
Thermal Bridging
This one is a little more complicated but bear with us because it’s essential to understand. Thermal bridging occurs when you create a path of least resistance between the heated internal space and the cold outdoors.
Insulation fills the gaps in the frame of a garden building, but the studs create a thermal bridge. Wood isn’t a great conductor of heat, so we can accept that we’re going to allow some heat to escape more easily. Steel, however, is on average 300 times more thermally conductive than softwood. This can significantly impact the thermal performance of a garden room.
In our article on vapour barriers, we explained the concept of interstitial condensation – condensation that occurs within the fabric of a building. The far higher thermal conductivity of steel increases the risk of condensation within the building’s roof, walls, and floor.
Using thermal breaks and helping to minimise cold bridging is essential in a steel-framed garden room.
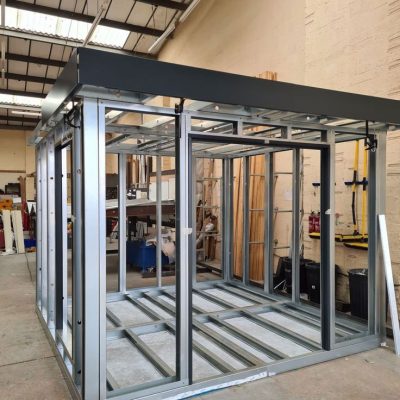
Will a steel frame corrode?
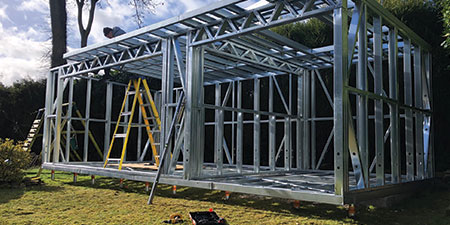
Steel may not rot like timber, but it can corrode when it comes into contact with moisture. Builders could opt for stainless steel instead since that doesn’t rust, but it’s often prohibitively expensive. Instead, manufacturers turn to galvanised steel.
Galvanisation is the process of coating steel with a layer of zinc. Zinc bonds well with steel and stops water and oxygen from reaching the underlying metal. While galvanised steel is expected to last for decades in most circumstances, there are factors that can speed up its deterioration, including:
- Overly humid environments – not usually a problem in the UK
- Coastal environments – high levels of salt in the air
- Contact with strong alkalis such as plaster or cement